Why Deciding On Professional Packaging Equipment Repair Services Matters
Why Deciding On Professional Packaging Equipment Repair Services Matters
Blog Article
Expert Solutions for Streamlined Product Packaging Equipment Maintenance and Repair Service Solutions
In the ever-evolving landscape of product packaging operations, maintaining the efficiency and reliability of tools is crucial. Professional remedies that utilize predictive upkeep methods and utilize IoT innovation provide a path to reduce unexpected downtime and decrease costs. These techniques not just concentrate on immediate repairs however likewise on expanding the lifespan of equipment with sophisticated diagnostic tools and organized repair work protocols. Additionally, tailored training programs empower professionals with the abilities necessary for swift and effective fixings. As companies look for to elevate their functional efficiency, one must think about just how these innovative techniques can transform maintenance practices.
Anticipating Maintenance Techniques
In the realm of product packaging devices maintenance, anticipating maintenance methods have actually arised as a transformative approach to lessening downtime and enhancing functional efficiency. By leveraging data-driven insights and advanced analytics, these methods permit for the timely recognition of potential failings before they happen, hence preventing unexpected break downs. Anticipating upkeep counts on condition-monitoring tools and IoT-enabled sensors that constantly evaluate the functional state of equipment. This real-time data collection facilitates the discovery of anomalies and wear patterns that may suggest unavoidable tools failure.
It enables companies to change from reactive to aggressive upkeep techniques, decreasing the frequency and intensity of tools failures. Predictive upkeep contributes to cost savings by decreasing the demand for emergency situation repair work and reducing production disruptions.
Tactically, firms that embrace anticipating upkeep get an one-upmanship by improving devices integrity and overall productivity. As technology remains to develop, the assimilation of predictive maintenance methods into product packaging devices upkeep programs will significantly end up being a conventional technique, driving lasting functional improvements.
Efficient Repair Work Procedures
Improving the repair service procedure is critical for preserving the functional efficiency of packaging tools. Efficient repair protocols ensure very little downtime, extend tools life expectancy, and optimize manufacturing routines. A structured approach starts with developing clear repair standards, that include step-by-step directions tailored to each certain devices kind. These standards must be readily accessible to maintenance personnel and regularly upgraded to include the latest technical improvements and industry requirements.
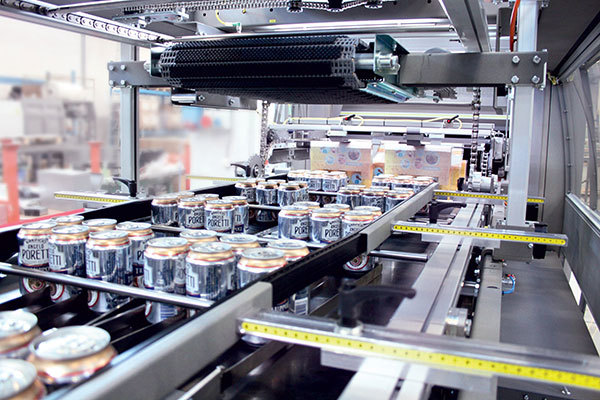
Educating upkeep teams in these procedures is equally important. Regular workshops and hands-on training sessions encourage employees to perform repair work quickly and precisely. Additionally, cultivating a culture of continuous renovation urges comments from specialists, leading to improvements out of commission approaches and protocols.
Advanced Diagnostic Tools
Advanced analysis tools give thorough understandings into the problem of product packaging equipment. For example, thermal imaging cams can detect overheating parts, enabling timely treatment. Resonance analyzers keep an eye on equipment vibrations, determining inconsistencies that might suggest mechanical faults, while ultrasonic detectors can determine air leaks or electric discharges that are not noticeable to the nude eye. These tools collectively add to an extra precise and educated maintenance strategy.
Additionally, integrating innovative analysis tools into upkeep protocols enables data-driven decision-making. The collected data help in anticipating tools failures and preparing targeted fixings. Services can assign resources more properly, lower maintenance prices, and improve the general dependability of their packaging systems.
Training and Skill Growth
The effectiveness of innovative diagnostic tools is substantially enhanced when paired with detailed training and skill growth for maintenance employees. Training programs tailored to the details needs of product packaging tools are important.
Skill growth campaigns can take various kinds, consisting of workshops, qualification courses, on-the-job training, and cross-training among employee. Stressing constant learning makes sure that specialists are abreast of the current technical advancements and upkeep techniques. In addition, buying skill advancement cultivates a society of technology and analytical, enabling upkeep teams to resolve tools issues proactively.
Additionally, well-trained personnel add to minimizing downtime and enhancing equipment performance, inevitably leading to raised functional effectiveness and cost savings. Developing an organized training strategy, straightened with business objectives, guarantees that the labor force is positive and experienced in keeping high requirements of devices treatment. This tactical strategy to training and ability growth is crucial in accomplishing streamlined maintenance operations in the product packaging sector.
Leveraging IoT and Automation
In today's swiftly evolving packaging automation, iot and sector are changing maintenance techniques, offering unmatched levels of performance and accuracy. By integrating IoT-enabled sensors and devices, packaging devices can currently connect real-time information pertaining to operational status and potential mistakes. This connection enables predictive maintenance, where problems are recognized and dealt with before they rise right into costly breakdowns, hence minimizing downtime and extending devices life expectancy.
Automation more boosts these abilities by automating regular upkeep tasks and diagnostics. With the implementation of automated systems, business can streamline their maintenance routines, decreasing manual treatment and the margin useful content for human error. Automated reports and notifies produced by IoT tools ensure maintenance teams are always educated, promoting an aggressive technique to devices care.
Moreover, the mix of IoT and automation facilitates smooth information evaluation, making it possible for better decision-making processes. By harnessing data analytics, companies can obtain understandings into tools performance patterns, enhance resource appropriation, and improve general functional effectiveness. This technological harmony not only decreases upkeep expenses yet likewise enhances productivity and reliability in product packaging operations. As the industry proceeds to advance, leveraging IoT and automation is crucial for preserving an one-upmanship in devices maintenance.
Verdict
The combination of predictive maintenance directory strategies, reliable repair service procedures, and progressed diagnostic tools significantly improves packaging devices repair and maintenance services. By leveraging IoT and automation, possible failures can be expected and resolved proactively, consequently minimizing downtime and prices. Structured training and skill growth for professionals even more guarantee the swift execution of essential repair services. This thorough technique not just extends the lifespan of equipment yet also improves efficiency and integrity, eventually maximizing operational effectiveness in packaging procedures.
In the realm of product packaging devices maintenance, predictive upkeep strategies have emerged as a transformative method to minimizing downtime and enhancing operational efficiency.Making use of advanced analysis devices is pivotal in enhancing the maintenance and my website repair work of packaging devices. In addition, spending in skill growth promotes a culture of development and analytic, making it possible for upkeep teams to attend to devices concerns proactively.
Automated reports and informs generated by IoT tools make sure upkeep teams are constantly educated, advertising a positive method to tools care.
The combination of predictive maintenance strategies, effective repair service procedures, and advanced analysis devices considerably boosts product packaging tools upkeep and repair work solutions.
Report this page